A common problem in industry is residual magnetism in parts after machining or working. Often parts stick together, proving difficult for additional processing. Another typical problem after machining is that parts can pick up swarf, and even washing can prove ineffective.
By demagnetising parts, the above problems can be alleviated.
There are various different ways to demagnetise something. But by far the most efficient and non-destructive method is to use a capacitive discharge demagnetiser.
A magnetic material is made up of separate domains which are aligned.
By applying a magnetic field we are able to switch the domains between north and south, and completely randomise the domains, resulting in a demagnetised object.
For more detailed description of how this works see our article on the principles of demagnetisation
We just completed an order for a capacitive discharge system for a client in the medical sector.
The parts to be demagnetised were very small and supplied in trays containing around 250,000 parts. Each individual part needed to achieve an overall level of ≤5 Gauss to pass QC.
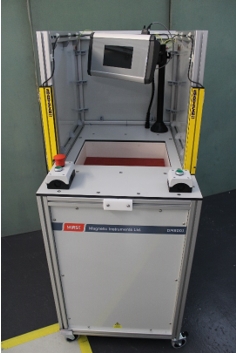
A tray of parts is loaded into the aperture in the worktop.
The demagnetizer is then configured using the touch screen interface.
When the two start buttons are pressed the demagnetizer charges a bank of capacitors, which discharge into the demagnetizing coil and create a “ringing” (decaying oscillation) magnetic field.
The system is fitted with light curtains, linked to a safety relay, to ensure safe and easy operation.
The image below shows the waveform captured via a pickup coil and PC oscilloscope during the testing procedure. This decaying oscillating field is key to successful demagnetisation.
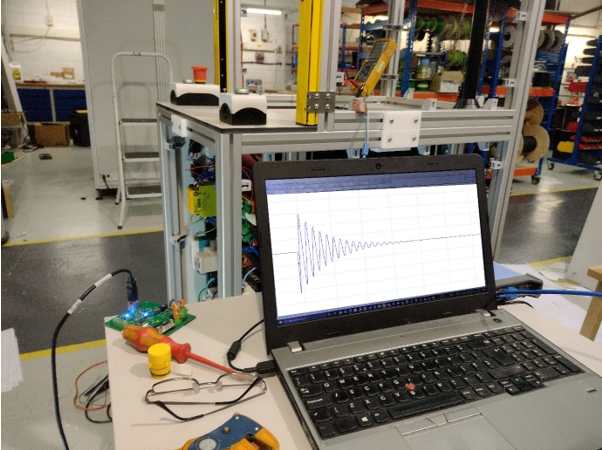
The whole process takes seconds from start to finish and is completely non-destructive.
If you would like to find out more about any of our de-magnetizing equipment please have a look on our de-magnetiser page